La soffiatura ha come obiettivo la rimozione di materiale particolato, ossido, materiale semi aderente e materiale eterogeneo (residui di saldatura, sabbia, etc.), presente nei sistemi vapore. Queste sostanze, formatesi durante le fasi di laminazione o apportate durante la costruzione degli impianti, possono arrecare gravi danni alle apparecchiature alimentate da tali tubazioni (turbine a vapore e valvole turbina) e causare seri problemi nel corso delle fasi preliminari di messa in esercizio degli impianti.
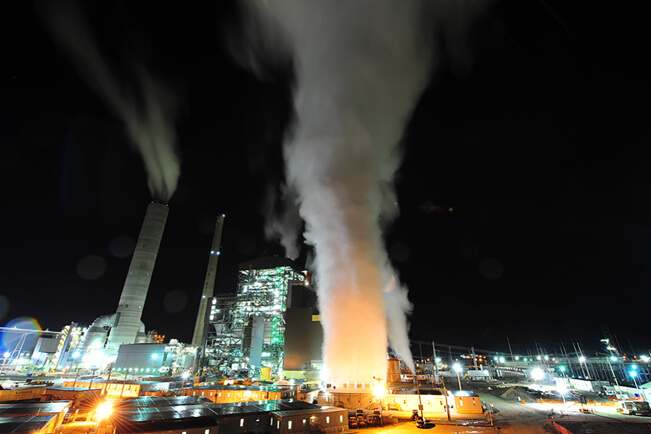
La misura del grado di pulizia è effettuato attraverso il cosiddetto DFR. Il DFR “Drag Force Ratio” è il fattore che misura la quantità di moto nelle condizioni di soffiatura rispetto a quelle di progetto.
Infatti, se ci si trova nelle condizioni di soffiatura “più severe” rispetto a quelle di esercizio (DFR > 1,2), si ottiene progressivamente la rimozione di tutte particelle veicolabili.
Le soffiature, quindi, sono attività propedeutiche alla messa in servizio di sistemi vapore, turbine a vapore, generatori di vapore, steam net distribution in raffinerie, etc. Tali attività sono strettamente necessarie in quanto i sistemi non completamente puliti prima della messa in marcia potrebbero pregiudicare l’integrità delle turbine e il funzionamento di valvole e strumentazioni, danneggiandosi.
La WCS è specializzata in questo tipo di attività fornendo tre diversi metodi di soffiatura in funzione della geometria dei sistemi, della disponibilità delle utilities, ai tempi a disposizione e a fattori economici. Le tre metodologie sono di analoga efficacia.
Le peculiarità di ogni tipologia di soffiatura sono descritte di seguito.
Soffiature in continuo con vapore a bassa pressione
Le caratteristiche di questo metodo sono:
- Grande efficacia
- Drastica riduzione dei tempi di esecuzione
- Bassa emissione sonora
Questo metodo permette di soffiare in continuo, per un tempo prolungato, a velocità prossima alla sonica, mantenendo il livello di rumorosità a valori bassi (<75 db a 30 metri dal silenziatore) e mantenendo una pressione alquanto contenuta (<7-8 bar).
Calcoli sono effettuati per verificare la velocità del vapore adatta a garantire la realizzazione della pulizia.
La possibilità di operare in continuo comporta la riduzione dei tempi di pulizia, dei costi e un risultato garantito.
Le soffiature a vapore sono un’attività critica durante il commissioning delle centrali termoelettriche e dei sistemi vapori in genere e, per questo motivo, è importante ridurre il più possibile il tempo richiesto per eseguire quest’operazione.
Adottando il “Silent Steam Blow” i risultati sono ottenuti in breve tempo utilizzando vapore surriscaldato a bassa pressione.
Vantaggi delle soffiature a vapore bassa pressione (quite steam blowing)
- Soffiatura in Continuo
- Basso livello di rumore <80 db
- Tempi di soffiaggio ridotti
- Raggiungimento grado di pulizia a bassa pressione
- Requisito di flusso di vapore ca. 30% -50% della capacità massima
- Non necessita di supporti speciali
- Non necessita di studi di Stress Analysis
- Benefici economici
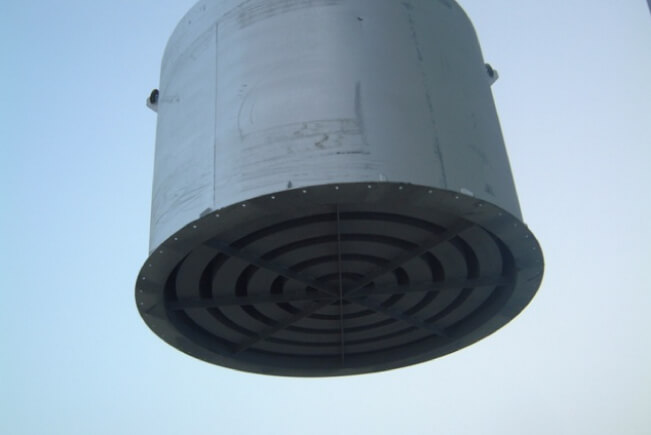
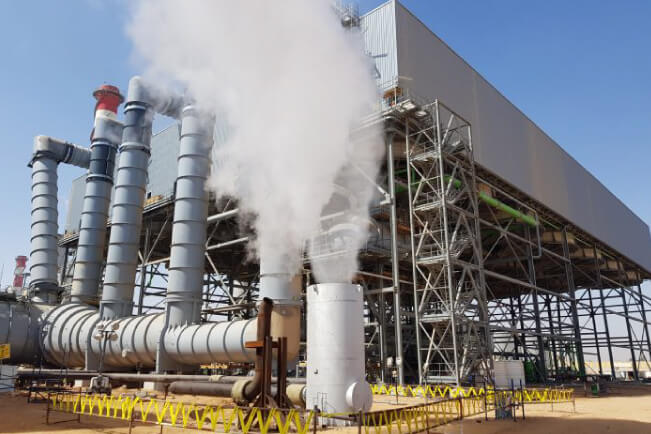
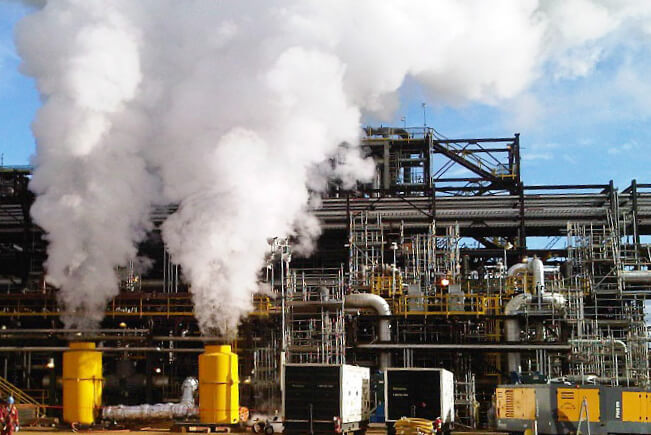
Soffiature con vapore in discontinuo (Soffiature a strappo)
Queste soffiature si eseguono con un metodo tradizionale, utilizzato spesso, nel passato, in centrali termoelettriche. Viene definito “a strappo” in quanto, una volta raggiunta la pressione prevista come da ingegneria, viene aperta la valvola di soffiatura (provvisoria) e, rapidamente, il vapore contenuto nel sistema viene rilasciato attraverso le linee provvisorie e il silenziatore. Per un breve lasso di tempo il vapore raggiunge il DFR (Il fattore che misura le condizioni di soffiatura) corretto, pulendo le linee di sistema. Questo metodo utilizza vapore a media e alta pressione, produce elevati shock termici e meccanici sui sistemi e, per questo, richiede calcoli ingegneristici accurati riguardanti le tubazioni temporanee (calcolo dello stress analysis) e tubazioni di conseguenza, con alto rating. Adottando questa metodologia, il valore del DFR viene raggiunto per pochi secondi/minuti per ogni apertura di valvola e ne consegue che i tempi necessari per raggiungere i gradi di pulizia richiesti siano più lunghi del metodo “quite stem Blowing” descritto in precedenza.
Gli svantaggi di questo metodo sono:
- Metodo Discontinuo
- Livello di rumore elevato> 120 db
- Elevato numero di cicli di soffiaggio
- Tempo di soffiaggio più lungo: 2-4 settimane per sistema pulito
- Linee di vapore soggette ad elevate forze meccaniche e stress termico
- Supporti speciali nelle linee di soffiaggio con relativi studi di Stress Analysis
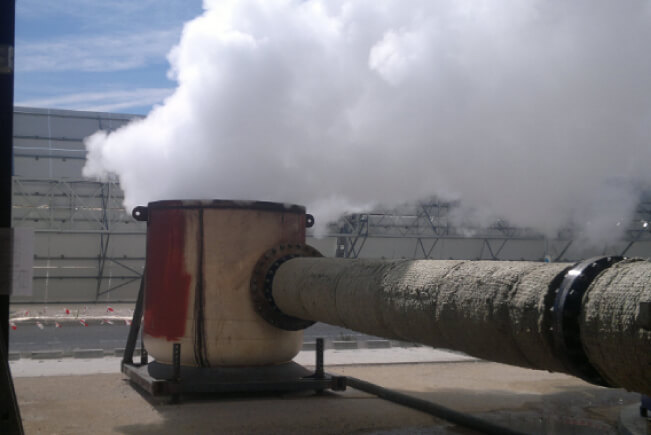
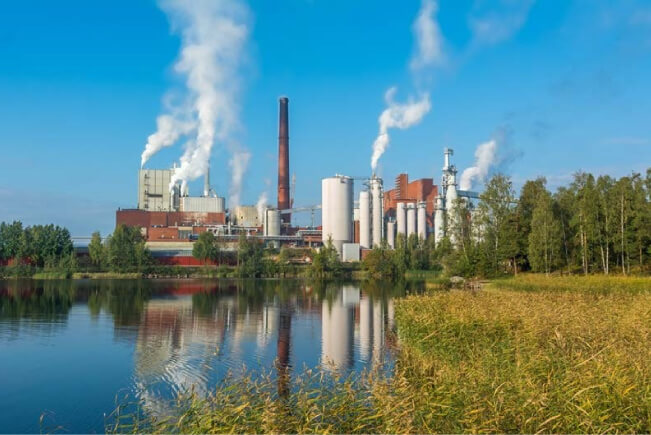
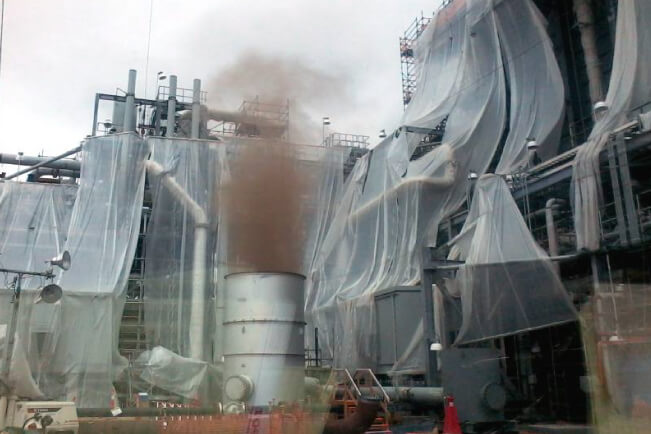
Soffiature con aria
Il vantaggio della soffiatura con aria deriva dal fatto che può essere realizzata senza avere la turbina a gas a disposizione. L’operazione quindi può essere eseguita ancora prima di avere il Turbogas commissionato e pronto alla produzione. Ciò consente di rendere la soffiatura indipendente dalla messa in servizio del turbogas e di poter anticipare le attività guadagnando giorni di produzione.
Il metodo si basa sull’effettuazione di cicli di soffiatura di tipo discontinuo, a freddo, nei quali, dopo una fase di pressurizzazione, si rilascia velocemente l’aria accumulata nei sistemi grazie all’apertura di valvole sacrificali ad apertura rapida. L’operazione, per essere efficace, deve essere ingegnerizzata, progettata ed eseguita in condizioni che garantiscano una quantità di moto maggiore di quella ottenuta in esercizio, ponendo sul percorso dei bersagli per verificare il grado di pulizia.
I vantaggi di questo metodo sono:
- Metodo discontinuo
- Cicli di soffiaggio ad alta pressione
- Crea istantaneamente alte portate
- Utilizzo di una valvola ad apertura rapida (valvola sacrificale)
- Elevate forze di resistenza con relativa fluidificazione efficace dei detriti
- Notevole riduzione dei tempi del programma di pulizia e successiva messa in servizio
- Può essere effettuata prima della messa in marcia dell’impianto